Injection Molding Services
Injection molding produces parts by forcing molten material into a mold where it cools and hardens to the mold’s shape.
eMachineShop offers cost-effective injection molding solutions whether you need a hundred pieces or a large production order.
- 50+ Materials.
- FREE Shipping in the USA.
- 100% Quality Guaranteed.

What is Plastic Injection Molding?
Plastic injection molding is a manufacturing process that involves injecting molten thermoplastic material into a mold, where it is then cooled and solidified to form a final product. This process is used across a wide range of industries, including automotive, consumer goods, medical, and electronics, to produce quality parts of varying complexity and size. The process is known for its capabilities for speed, precision, and efficiency and has become one of the most popular manufacturing services for the production of plastic parts. When engineering molds for injection molding services, designers need to keep in mind limitations, appearance, strength and economics.
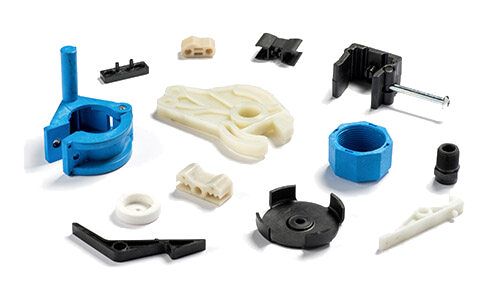
Advantages of Injection Molding
Injection molding offers:
- Large volume runs of simple or complex uniform parts with tight tolerances.
- Wide variety of materials are compatible with the injection molding process. As a result, it is easy to get parts colorized.
- Compared to 3D printing or CNC machining, the injection molding process is much faster when it comes to production in mass quantities.
- Reliable manufacturing for repeated production runs after the prototyping phase has concluded.
Disadvantages of Injection Molding
- High startup costs
- Not cost effective for low-volume runs
- Long initial lead times as the mold needs to be manufactured and tested
- Alterations to the initial design can be expensive and add to turn around time
How modern Plastic Injection Molding works
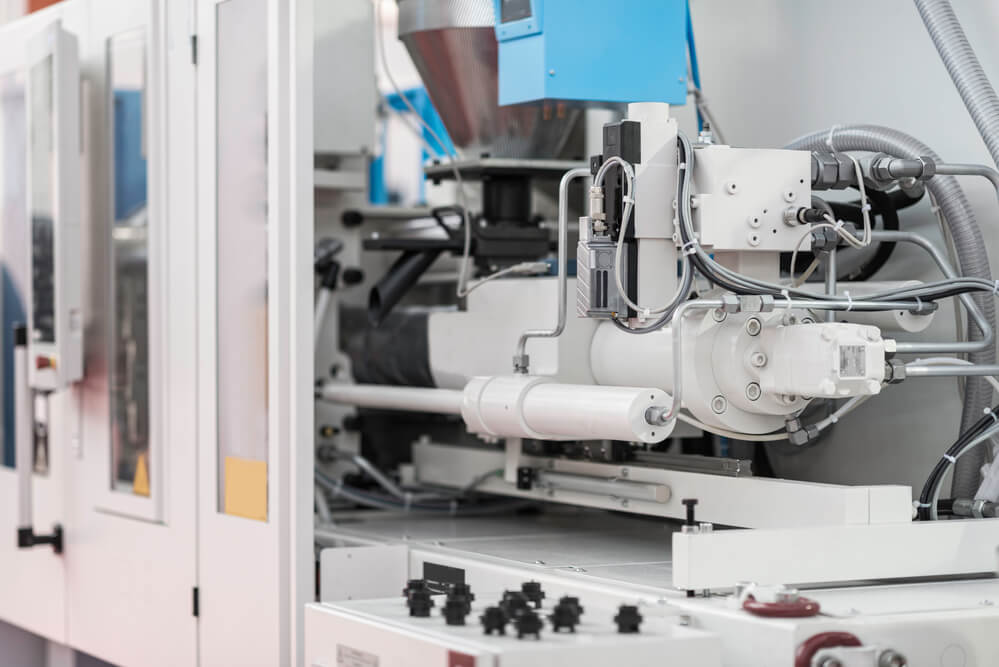
Injection Molding for a custom manufacturing project is an intricate and complex process and differs from other common manufacturing processes such as CNC machining and prototyping. First, a mold of the part must be manufactured from a CAD drawing. CNC machining creates a physical model, typically in steel or aluminum. Once the metal mold has been manufactured it is inserted in the injection molding machine to be set up for production. The metal mold is typically designed in halves so the finished part can be easily removed once the material has finished the cooling process.
An injection molding machine has three main parts: the injection unit, the mold, and the clamp. Thermoplastic granules or pellets go into a hopper which feeds into the barrel of the injection unit. Inside the barrel, a reciprocated screw transports the granules forward. Heater bands that are wrapped around the barrel are used to warm up the plastic granules. As the thermoplastic granules are moved forward by the screw, they gradually melt and are entirely molten when they reach the front of the barrel. Once enough molten plastic is in front of the screw it drives forward into the empty part of the mold called the cavity image. The molten plastic quickly cools and solidifies, the mold opens, the part is ejected, the mold then closes, and the process repeats.
Injection Molding Terminology
It is important to understand industry related terms when learning how to properly design a part for plastic injection molding.
Below are commons terms used in reference to injection molding:
- Mold: The tool or die used to shape the plastic material into the desired form.
- Injection Molding Machine: The machine that is used to inject the molten plastic into molds.
- Clamping Unit: The part of the injection molding machine that holds the mold shut during the injection process.
- Injector: The part of the injection molding machine that injects the molten plastic into the mold.
- Plasticating Unit: The part of the injection molding machine that melts and mixes the plastic material before it is injected into the mold.
- Runner: The channel through which the molten plastic flows from the injector to the mold.
- Gate: The point where the molten plastic is inserted into the mold.
- Ejection System: The system that is used to remove the finished part from the mold.
- Flash: Excess plastic that is extruded from the mold when the parts are being formed.
- Backflow: The flow of plastic material back into the injector as a result of the pressure drop in the mold.
- Resin: The raw plastic material that is used in the injection molding process.
- Cycle time: The time it takes to complete one injection-molding cycle, including the time to fill the mold, cool the part, and eject it from the mold.
- Shrinkage: The reduction in size of a plastic part as it cools and solidifies.
- Draft angle: An angle that is added to the sides of a part to facilitate the removal of the part from the mold.
- Tolerance: The allowable deviation from the specified dimensions of a part.
Design Tips for Injection Molded Parts
Design Tips for Molding
Plastic injection molding is a widely used manufacturing process for the production of parts of various shapes and sizes. However, designing parts for injection molding can be challenging, as there are many factors to consider in order to achieve a successful outcome. From material selection, to wall thickness, gate location, and post-molding operations, every aspect of the design needs to be carefully thought out in order to produce a high-quality and cost-effective part.
Simplicity is Important:
There are many factors that can quickly complicate an injection molding project. By keeping your design simple you can avoid many complications that may arise in the manufacturing process. Some examples of simplicity in design are avoiding sharp inside corners, undercuts, and deep recessed cavities, which can all hinder the ejection process from the mold cavity and quality of the final product.
Use proper draft angles:
Designing proper draft angles is an important part of injection molding design because it allows easier and more efficient part removal from the mold. If a part design does not account for removal from the mold, the part can stick to the mold making it difficult to remove and potentially damage the parts upon removal. Both of these setbacks increase manufacturing costs and a lower yield of parts within the intended tolerance.
In general, it is best to avoid 90 degree angles in injection molding designs since they are not practical with the manufacturing process. However, a proper draft angle can be used to avoid these complications. A draft angle is a small incline of the surface of the part that makes it easier to remove from the mold. Even a one degree adjustment to a vertical surface of the part can prevent parts from sticking to the mold, prevent warping, and minimize unwanted flashing on surfaces.
Plan for shrinkage:
Since the plastic injection molding process involves heating plastic to fill a pre-existing mold, it is important to keep in mind that plastic decreases in volume as it cools and solidifies. This process is called shrinkage. Shrinkage rates will vary based on the type of plastic material that is being used, wall thickness of the part, and the overall temperature of the mold.
Shrinkage can create numerous issues during the injection molding process, such as warping, cracking, or flashing. Warping occurs when parts cool unevenly causing unwanted bends or twists. Cracking occurs when parts cool too quickly which creates stress points that are severely weakened. Flashing occurs when plastic leaks out of the mold cavity and cools along the parting line.
In order to minimize complications that come with shrinkage, part designers must take many factors into account, such as the shrinkage rate of the intended plastic material and designing the mold cavity with slightly oversized dimensions. Both of these considerations allow for the part to shrink to its correct size once it has cooled and solidified.
Think about the gate location:
Gate location is where the melted plastic is injected into the mold in injection molding. Since the gate is the point of entry of plastic in a mold, it needs to be designed and placed carefully to ensure a smooth and efficient molding process.
Gate location is important because it affects the quality and consistency of the final part. A poorly placed gate location can result in defects such as uneven cavity filling, sink marks, or flashing. Poor gate positioning may also result in cosmetic flaws or imperfections if not properly taken into account. Typically gates are located in non-visible areas to avoid any cosmetic issues with the outer surfaces.
Another important factor of designing a gate location is understanding that it affects the flow of plastic into molds, the filling time, the cooling time, and accommodating pressure releases from the heating and cooling processes. An optimally designed gate location would ensure that the melted plastic is evenly and efficiently distributed throughout the mold which would result in a consistent and high-quality final product.
Consider the material:
When designing a part for an injection molding project, choosing the proper material can have a significant effect on the outcome of the final part. Since injection molding can utilize a large array of different plastic materials, it is important to consider which plastic material is suited for your design, both functionally and cosmetically. The properties of a plastic material can determine its longevity and functionality in various chemical, temperature, and pressure environments, as well as dimensional stability, surface finish, and overall aesthetics.
Some important factors to consider when choosing the proper plastic material for your injection molding project are mechanical properties, temperature resistances, chemical resistances, dimensional stability, surface finishes, and even recyclability. Before choosing a material to be molded, it is important to confirm whether or not the functionality of the final part would be hindered by particular properties of the base plastic material.
Make use of ribs and bosses:
Ribs and bosses are typically used in injection molding designs to add strength and rigidity to parts and reduce the chances of having it warp or break. When ribs or bosses are placed correctly, they can increase the structural integrity of a part and distribute pressure points more evenly across a part.
Ribs are raised features which are added to increase the stiffness and strength of a part. They are typically added to walls or other thin sections of a part to prevent warping or other deformations. These ribs also allow for even distribution of loads across a part which reduces the formation of stress points and cracks.
Bosses are another raised feature that are added to designs to provide locations for fasteners, screws, bolts, or other mating surfaces for other parts.
Both of these features have the capabilities of adding to the overall structural integrity of a part but also to produce a more aesthetically pleasing and functional design. When designing these features, it is important to keep in mind the thickness, size, and location of their placement. When properly designed, ribs and bosses can minimize the chances of warping, cracking, and flashing while also improving the overall quality and consistency of the part.
Wall thickness should be consistent:
When designing a part for plastic injection molding, consistency among wall thicknesses is important because it helps ensure that the plastic will cool and solidify evenly, which reduces the risk of defects, such as warping or cracking. When a part has an uneven or inconsistent wall thickness, the thicker sections cool and solidify more slowly compared to thinner wall sections. This design flaw can lead these thicker walls to warp or crack as they cool since the thinner sections have already been solidified and molded.
Having consistent wall thickness also helps provide the final parts with dimensional stability and reduces the risk of shrinkage or warping. Consistent wall thickness typically results in better surface finish and overall consistency in terms of dimensions and shape. Features such as ribs and bosses can also be used to strengthen certain sections so the walls can stay consistent, provide structural integrity and improve the overall quality of the molded parts.
Consider post-molding operations:
Not all parts are designed to be used as produced. Many parts undergo secondary machining services to make the final product, such as trimming, sanding, polishing, painting, assembling, and packaging. Even if a part is not meant for a secondary machining service, it might become necessary due to short-sighted design mistakes. For example, if a part is affected by flashing due to shrinkage or inconsistent wall thickness, it may have to undergo trimming or sanding to remove excess materials which adds to manufacturing costs and delays production.
By considering post-molding operations in the design or prototyping process, it makes it possible to optimize the engineering of the parts and the molds, to minimize the need for additional machining services and steps.
Popular materials used in plastic injection molding
There are many different types of plastic materials that can be used in injection molding, each with its own unique properties. As a result, these materials will vary in popularity in different industries. The same material used for the automotive industry may not be suited to the medical industry, etc.
Some of the most popular materials used in injection molding include:
- Polyethylene (PE) – This is a versatile plastic material that is widely used in injection molding. It is known for its excellent chemical resistance, low cost, and ease of processing. PE is widely used in medical industries.
- Polypropylene (PP) – This material is known for its excellent strength, high melting point, and good chemical resistance. It is commonly used to produce parts such as automotive components, packaging materials, and household items.
- Polystyrene (PS) – This material is known for its low cost, high clarity, and good resistance to impact. It is commonly used to produce parts such as packaging materials and household items.
- Acrylonitrile-Butadiene-Styrene (ABS) – This material is known for its excellent impact resistance and toughness. It is commonly used to produce parts such as automotive components, toys, and electronic housings.
- Polyvinyl chloride (PVC) – This material is known for its excellent chemical resistance and durability. It is commonly used to produce parts such as pipes, fittings, and electrical conduit.
- Polycarbonate (PC) – This material is known for its high strength, high heat resistance, and excellent optical properties. It is commonly used to produce parts such as safety glasses, automotive lighting, and electronic housings.
- Nylon (PA) – This material is known for its high strength and wear resistance, as well as its low coefficient of friction. It is commonly used to produce parts such as gears, bearings, and mechanical parts.
Material selection is an important factor in the design of parts for plastic injection molding services. The properties of the plastic material used can have a significant impact on the final product, including its strength, durability, appearance, and cost.
- Strength: Different plastics have varying levels of strength, which is important to consider when designing parts that will be subject to stress or loads. For example, polycarbonate and nylon have high strength, making them suitable for applications such as gears and mechanical parts.
- Durability: Plastic materials can have varying levels of resistance to wear, impact, heat, chemicals and UV, which is important to consider when designing parts that will be exposed to harsh environments. For example, polyethylene and polypropylene have good chemical resistance, making them suitable for applications such as tanks and containers.
- Appearance: Plastic materials can have varying levels of transparency, color and surface finish, which is important to consider when designing parts that will be visible in the final product. For example, polystyrene and ABS have high clarity, making them suitable for applications such as light covers and displays.
- Cost: Different plastics have varying costs and availability, which is important to consider when designing parts that will be produced in high volume. For example, polyethylene and polypropylene are relatively inexpensive and widely available, making them suitable for applications such as packaging, consumer goods, appliances and medical supplies.
Compatible Materials
Plastic injection molding and environmental impact
Plastic injection molding is considered to be a relatively environmentally-friendly manufacturing process for several reasons, such as:
- Recyclability: Many plastics used in injection molding can be easily recycled, reducing the amount of waste in landfills and conserving natural resources.
- Energy efficiency: Modern plastic injection molding machines are highly energy efficient, using significantly less energy than other manufacturing processes.
- Durability: Plastic products produced by injection molding are typically very durable, meaning they last a long time and therefore don’t need to be replaced as often.
- Lightweight: Plastic products are typically lightweight, which reduces the energy required to transport them.
- Consistency: Injection molding allows for consistent and uniform parts, reducing the need for additional materials and minimizing waste.
- Minimal waste: The injection molding process generates very little waste material, as the majority of the plastic is used in the molding process. Any waste generated can be recycled or reused.
- Low emissions: Many plastic injection molding facilities employ advanced technologies and processes to minimize emissions and waste, making them relatively environmentally friendly.
- Versatility: Plastic injection molding is a versatile process that can be used to create a wide variety of parts and products, which can often be used in place of products made of other materials, such as metal or wood, which require more energy and resources to produce.
However, it’s worth noting that not all plastics are equally environmentally friendly, and some types of plastics have a greater environmental impact than others. Also, the environmental impact of plastic injection molding depends on the entire life cycle of the product, including the sourcing, manufacturing, transportation and disposal of the product.
Plastic Injection Molding and 3D Printing
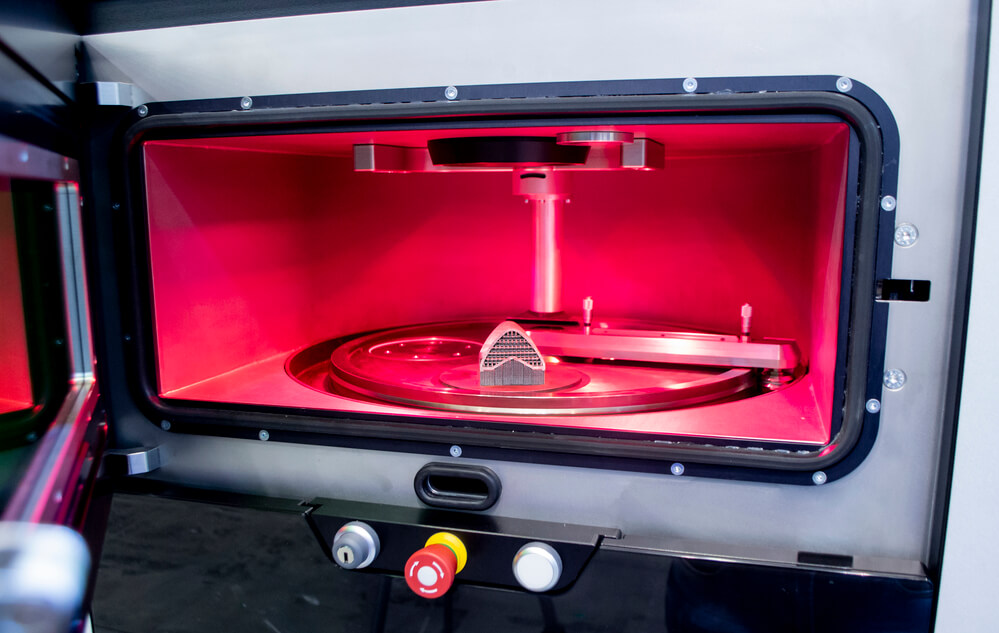
Although plastic injection molding and 3D printing both use raw plastic materials, they have distinctly different advantages. 3D printing allows customers to design and produce a product much faster than for injection molding. Injection molding, on the other hand, has a much longer setup time and tooling cost but produces parts faster and more economically. 3D printing requires less tooling, engineering, and setup than injection molding, making it a quicker and more cost-effective option for producing smaller quantities of products or custom prototyping.