Introduction to Anodizing
In the vast universe of metal finishing, aluminum anodizing services shine as a stellar constellation, offering an extraordinary blend of beauty and resilience. Anodizing transforms the surface of aluminum, not merely enhancing its appearance but fortifying it with a durable, corrosion-resistant finish that stands the test of time and elements. This introduction to anodizing isn’t just a technical overview; it’s a gateway into understanding how aluminum—an abundant and versatile metal—can be elevated to meet the demands of various applications, from the sleek exteriors of aerospace marvels to the intricate components of electronic gadgets.
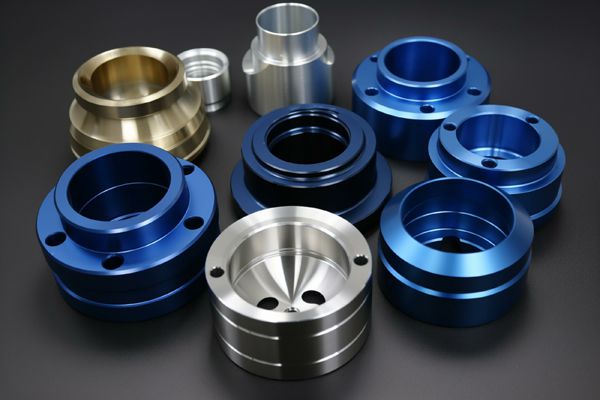
Aluminum Anodizing Services: Crafting Durability with Precision
The choice of aluminum anodizing services is a testament to precision and quality. Specialized services offer custom aluminum anodizing solutions tailored to the unique requirements of different industries. Aerospace components demand finishes that can endure the harsh realities of space exploration. Automotive parts require a blend of durability and aesthetic appeal, ensuring that vehicles not only perform well but also captivate onlookers with their luster. Electronics manufacturers seek finishes that provide protection against corrosion and wear, ensuring the longevity of devices in the hands of consumers. The decision to select a specialized aluminum anodizing service isn’t merely practical; it’s strategic, ensuring that every finished product not only meets but exceeds the stringent standards of its intended application.
Electronics Industry Example: Anodized Laptop Cases
Aluminum Anodizing Services play a crucial role in the production of laptop cases. These services enhance the durability and resistance of aluminum cases to daily wear and tear, including scratches and dents.
Benefit: Anodized aluminum finishing provides a sleek, attractive appearance while ensuring the laptop case withstands the rigors of daily use. This durability is essential for protecting valuable electronic components.
Aerospace Industry Examples:
Aircraft Control Panels
Custom Aluminum Anodizing processes are utilized for aircraft control panels, tailoring the anodizing to meet specific requirements for durability and aesthetics in the cockpit environment.
Benefit: The anodized aluminum finishing ensures that control panels can endure the harsh conditions of flight, including exposure to UV light and potential chemical spills, while maintaining clear legibility of controls and indicators.
Aircraft Fuselage Panels
Benefit of Anodizing: Anodizing these panels via the Aluminum Anodizing Process significantly increases their resistance to the harsh environmental conditions faced at high altitudes, including extreme temperatures and UV exposure.
Anodized Aluminum Finishing: Provides a durable surface that withstands the rigorous wear and tear during flights while maintaining the aesthetic integrity of the aircraft’s exterior.
Aircraft Landing Gear
Benefit of Anodizing: Custom Aluminum Anodizing offers enhanced wear resistance and protection against corrosion from exposure to various chemicals and environmental conditions.
Anodized Aluminum Colors: While the color may not be the primary concern for structural components like landing gear, the option to add color coding can facilitate quick identification and maintenance checks.
Automotive Industry Examples:
Automotive Trim and Accessories
Benefit of Anodizing: Accessories and trim pieces benefit from Aluminum Anodizing Services by gaining a protective layer that guards against weathering and corrosion, extending the lifespan of these parts even under severe weather conditions.
Anodized Aluminum Finishing: Besides the protective benefits, the anodizing process enhances the visual appeal of automotive accessories, with Anodized Aluminum Colors offering customization options to match or accent the vehicle’s aesthetic.
Engine Components:
Benefit of Anodizing: The Aluminum Anodizing Process is crucial for engine parts, providing a heat-resistant coating that stands up to the extreme temperatures and pressures within an automotive engine environment.
Custom Aluminum Anodizing: Tailors the surface properties of engine components for specific performance requirements, improving durability and efficiency while potentially adding a layer of color identification for complex assemblies.
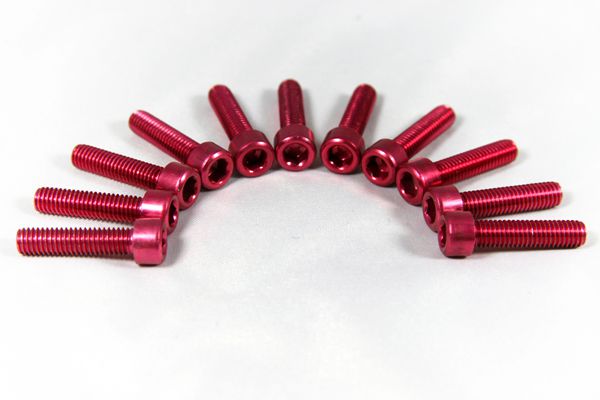
Understanding the Anodizing Process: A Technical Deep Dive
The aluminum anodizing process is a marvel of modern electrochemical engineering. It transforms the surface layer of aluminum into a hard, durable anodic oxide finish. This isn’t a surface coating but a deep integration into the aluminum itself, providing unmatched durability and resistance to corrosion. The process involves submerging aluminum in an electrolyte and passing an electric current through it, resulting in the formation of the oxide layer. This layer is fully integrated with the aluminum substrate, making it part of the metal itself. For those intrigued by the scientific and technical depths of the anodizing process, a treasure trove of information can be found in the MDPI article on the subject, offering a comprehensive look at the mechanisms that make this process a cornerstone of modern aluminum finishing.
Anodizing Colors: A Rainbow of Possibilities
The world of anodized aluminum colors is as diverse as it is dazzling. Through the anodizing process, aluminum surfaces can be imbued with a wide array of colors, from the deepest blacks to the most vibrant reds and blues. This coloration process is not merely cosmetic; it’s a fusion of color and metal that resists fading and wear over time. The ability to customize the color of anodized aluminum opens up a universe of design possibilities, allowing manufacturers and designers to create products that stand out not only for their performance but also for their aesthetic appeal.
Benefits of Aluminum Anodizing: Beyond the Surface
Aluminum anodizing services offer a plethora of benefits that extend far beyond the surface. The anodized finish significantly enhances the corrosion resistance of aluminum, ensuring that products can withstand harsh environments and conditions. The process also increases surface hardness, making anodized aluminum comparable to sapphire in terms of durability. Furthermore, the aesthetic enhancements provided by anodizing—be it through natural metallic sheens or vibrant colors—add significant value to products, making them more appealing to consumers. Additionally, aluminum anodizing is an environmentally friendly process, utilizing less harmful chemicals and producing less waste compared to traditional metal finishing techniques.
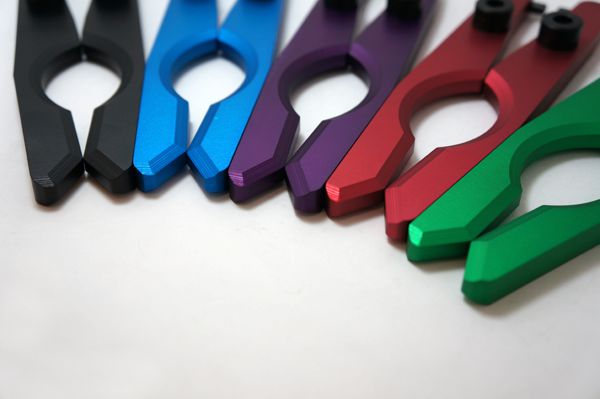
Corrosion Inhibition
One of the paramount benefits of aluminum anodizing is its remarkable ability to inhibit corrosion. The anodizing process thickens the natural oxide layer on the surface of aluminum parts, providing a barrier that is much more resistant to corrosion caused by environmental exposure. This protective layer is integral to the aluminum’s durability, especially in applications prone to harsh conditions, such as marine environments or areas with high pollution levels.
The duration for which corrosion is inhibited after aluminum anodizing greatly depends on the thickness of the anodized layer and the specific environmental conditions the part is exposed to. Generally, thicker anodized coatings offer longer protection, with some treatments designed to last for decades under normal conditions. However, for precise metrics on the longevity of corrosion inhibition, consulting technical specifications provided by the Aluminum Anodizer’s Council or industry standards like those from the Aluminum Association can offer more detailed insights.
Surface Hardness Improvement
Another significant advantage of anodizing aluminum is the improvement in surface hardness. The anodized layer that forms during the process is extremely hard, making the surface of aluminum parts nearly as durable as sapphire, the second hardest natural substance after diamond. This increased hardness translates to enhanced resistance against scratches and wear, extending the service life of the aluminum part.
The specific degree to which surface hardness is improved can vary based on the anodizing method used and the desired finish. For example, Type III, or hardcoat anodizing, produces a much thicker oxide layer, significantly increasing the surface hardness compared to Type II anodizing, which is more commonly used for achieving various aluminum anodizing colors and aesthetic finishes.
Aesthetic Enhancements with Aluminum Anodizing Colors
Beyond the practical benefits, aluminum anodizing beautifully accentuates aluminum parts with a wide spectrum of colors without compromising the metal’s natural luster. These aluminum anodizing colors are achieved through either organic dyes or electrolytic coloring processes, allowing for a vast range of hues that are both vibrant and fade-resistant. The coloration process occurs during anodizing, ensuring that the color is integral to the oxide layer and does not peel or chip away like paint or other surface treatments. This ability to combine aesthetic appeal with functional durability makes aluminum anodizing a preferred choice for many applications.
Reference for Corrosion Inhibition and Surface Hardness
For those interested in delving deeper into the specifics of corrosion inhibition and surface hardness improvements through anodizing, the Aluminum Association’s and the Aluminum Anodizer’s Council offer comprehensive data and guidelines. Additionally, an article by Herman Terryn offers an excellent technical discussion of the impact of aluminum anodizing.
In summary, the benefits of aluminum anodizing extend well beyond the surface, offering significant improvements in corrosion resistance, surface hardness, and aesthetic appeal through vibrant aluminum anodizing colors. This process not only enhances the durability and longevity of aluminum parts but also contributes to their environmental sustainability by utilizing less harmful chemicals and producing minimal waste.
Conclusion: Embracing Excellence in Aluminum Anodizing
As we conclude this journey through the world of aluminum anodizing, it becomes clear that choosing quality aluminum anodizing services is not just about ensuring the durability and aesthetic appeal of aluminum products. It’s about embracing a commitment to excellence, innovation, and sustainability. Whether for aerospace, automotive, electronics, or any other industry, aluminum anodizing offers a path to enhancing the natural beauty and functionality of aluminum, ensuring that it meets the challenges of modern applications with grace and resilience.
In a world where the demands on materials are ever-increasing, aluminum anodizing stands as a beacon of progress, offering solutions that are as durable as they are beautiful. It’s a choice that reflects a forward-thinking approach to material science, one that values both form and function. As we look towards the future, the role of aluminum anodizing services in shaping the next generation of products is not just promising; it’s paramount.
Embrace the full potential of aluminum with eMachineShop’s anodizing services. Dive into a world where color meets durability and let us help you unlock the true beauty and strength of your aluminum parts. Contact us today to explore the endless possibilities of custom aluminum anodizing.