Sheet Metal Fabrication
Sheet Metal Fabrication is a subtractive manufacturing process by which sheet material is cut to create parts.
eMachineShop offers cost-effective sheet metal and sheet plastic fabrication services whether you need a single part, batch of prototypes, or full production order.
- 50+ Materials.
- FREE Shipping in the USA.
- 100% Quality Guaranteed.

Sheet Metal Cutting Processes
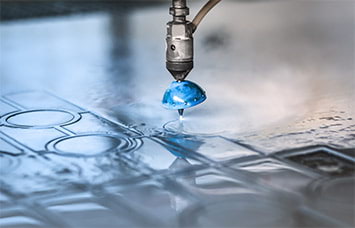
Waterjet Cutting
Waterjets mainly cut sheet material into 2D parts using a high-pressure stream of water and abrasive. Waterjet cutting is suitable for most materials and yields clean edges.
Sheet Metal Fabrication Advantages
Sheet metal fabrication has several advantages over other CNC machining methods:
- Fast turn times – lower setup time allows faster delivery
- Economical – the process is usually more economical than machining for both prototyping and production
- Secondary operations of bending allows creating intricate parts at minimal extra cost.
Sheet Metal Fabrication Applications
Custom sheet metal manufacturing is used in a variety of applications such as, aerospace, automotive, medical, consumer products, scientific instruments, and electronic devices. Sheet metal manufacturing can be customized to create a wide range of parts, including brackets, covers, frames, enclosures, and housings. Sheet metal fabrication process can create complex and intricate shapes with accuracy and precision. The manufacturing process is cost-effective, accurate, and repeatable, making it a great choice for many industrial and manufacturing applications.
What is Sheet Metal Fabrication?
Sheet Metal fabrication is a manufacturing process that converts sheets of metal into custom functional parts. The process typically involves removing material from the sheet to form the basic shape and then may involve secondary steps, such as bending, to create more complex 3D shapes such as pans, boxes and brackets. The sheet metal fabrication process typically involves CNC (Computer Numerical Control) machines that guide the cutting or forming process automatically under computer control. The manufacturing process makes precision parts with simple or complex shapes by automating the cutting process.
In CNC machining, a computer program written in the G-code language, is used to control all aspects of the machine. The G-code tells the machine what to do at each step, including motions, speeds and feed rates. The G-code is typically created using computer-aid-manufacturing (CAM) software which works from CAD software. The G-code is uploaded to the machine for processing.
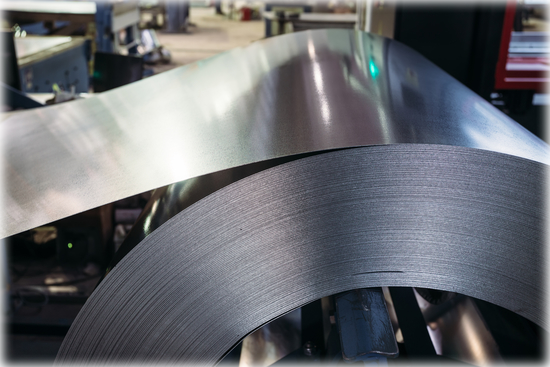
eMachineShop Made Sheet Parts
How does sheet metal fabrication work?
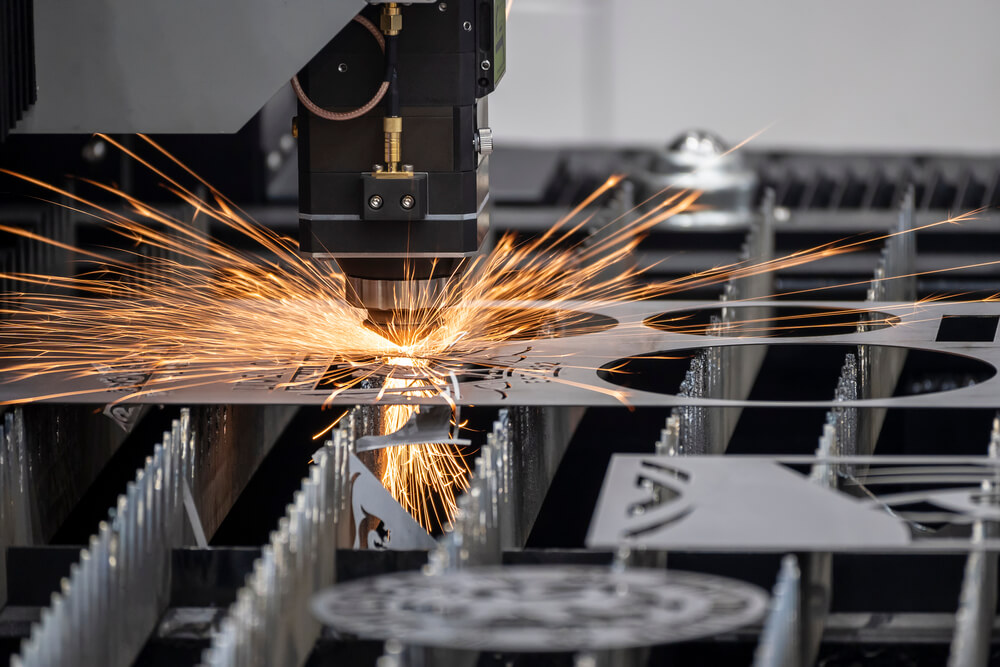
Raw material in sheet form is first mounted in a machine on a “workholding device” typically using clamps or gravity to hold the material that is being machined. The CNC machine reads the G-code program to move cutting tools in a predetermined sequence. The cutting sheet metal tools move along the X, Y and sometimes Z axes. In more advanced machines there are even more axes of movement. This allows the CNC machine to produce parts with complex geometries and high levels of precision.
During the machining process, the machine tools remove material from the workpiece by a cutting action. As the material is removed, the cutter moves to the correct position for each machining operation, as specified by the G-code. This process is repeated until the desired part has been fully fabricated.
Types of sheet metal fabrication
There are several different methods of sheet metal fabrication, each of which has its own advantages, such as speed, accuracy, and cost-effectiveness, making them useful for a variety of applications and sheet metal materials.
- Laser cutting is a type of fabrication that uses a focused laser beam to cut and shape materials.
- Waterjet cutting is a type of fabrication that uses a high-pressure stream of water to cut and shape materials.
- Plasma cutting uses gas and electricity to cut through the sheet metal.

Designing for sheet metal
Here are some design tips for parts that will be fabricated from sheet metal:
Complex shapes and features may be difficult or time consuming to machine, so it is generally best to keep the design as simple as possible.
Tolerances are the allowable variations in the size and shape of a part. It is important to use appropriate tolerances for sheet metal fabrication, as overly tight tolerances may be difficult to achieve and may result in increased production costs. Tolerances for flat parts will be tighter than parts with bends. Parts with multiple bends create a tolerance stack that should be carefully considered.
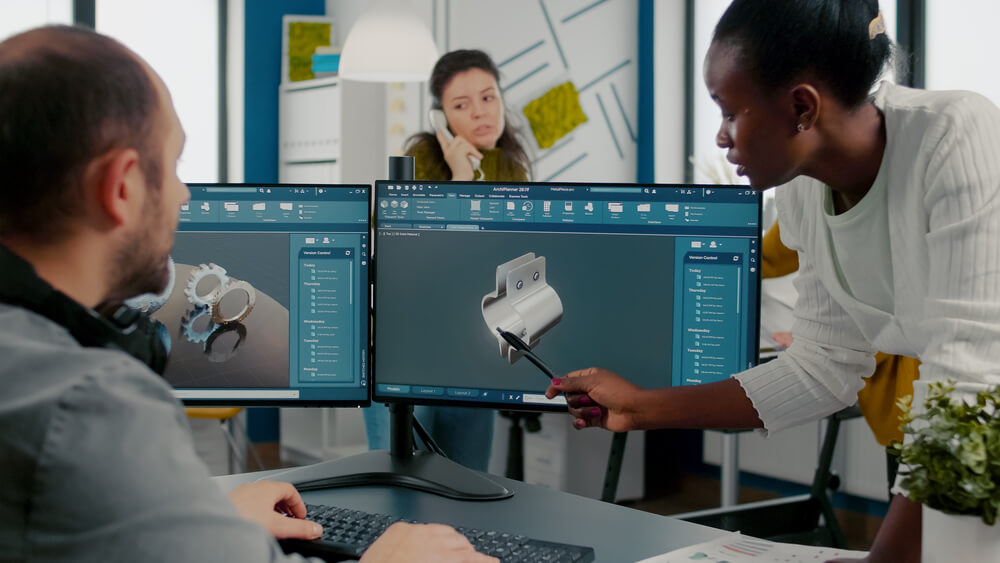
Estimating Sheet Metal Fabrication Costs
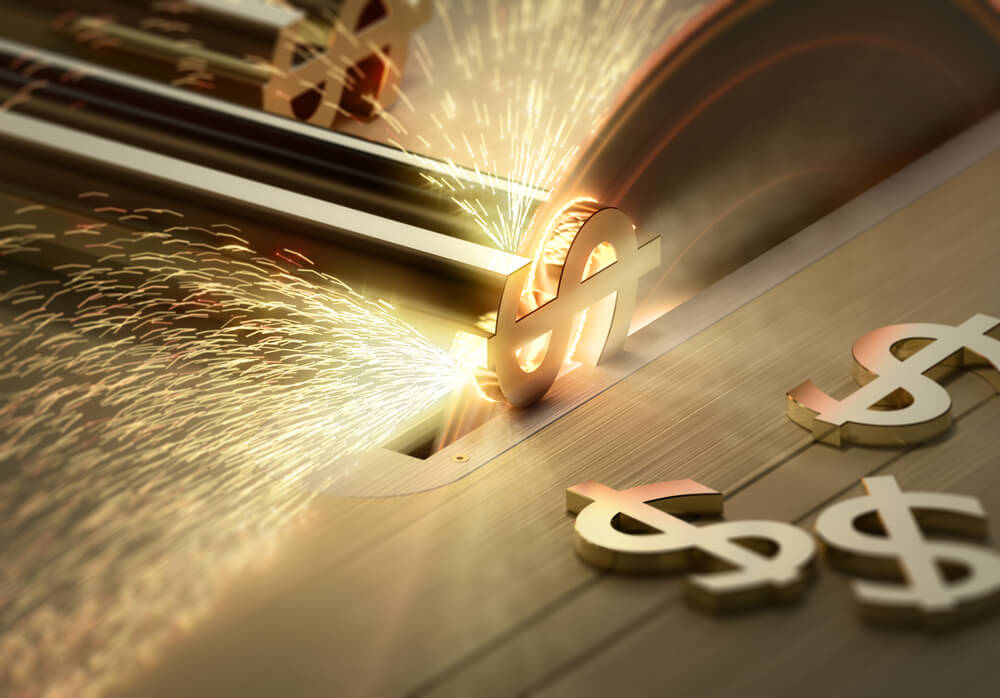
There are a few things you can try to reduce the cost of parts fabricated from sheet metal:
- Consider using a less expensive material. Different sheet metal materials have different price points, and switching to a less expensive material could help reduce the overall cost of your parts.
- Some processes are faster and more efficient than others, which can result in lower production costs. For example laser cutting is usually faster than waterjet.
- Most suppliers have lower costs as the order quantity goes up, so if you’re able to order a larger quantity of parts at once, you will likely get a better price. This is because setup costs must be amortized.
- Consider nesting for designs with multiple parts. Nesting is the process of arranging parts on a sheet of material in the most efficient way possible, allowing for multiple parts to be cut from a single sheet, reducing the amount of metal used. This can save time and money during the manufacturing process.
Sometimes small changes to the design of a part can significantly reduce the cost of production.
Upload your file
for a fast quote
Get a Quote
No CAD file?
Draw it easily with our CAD
GET FREE CAD
Materials that can be fabricated
Sheet metal fabrication can use a variety of metals such as steel, aluminum, brass, copper, stainless, titanium, and many other metal sheets to form custom parts. Some sheet metal fabrication machines, such a waterjet, are designed to handle thicker metal materials, while others are optimized for thinner sheet metal materials, such as laser cutting.
Compatible Materials
Which materials are good for bending?
Most metals can be bent but some are more likely to fracture due to the stresses that occur during bending. Aluminum is normally an excellent choice for bending but the popular 6061 alloy can be problematic if the thickness and bending radius are not within scope as the material can crack due to its hardness. Aluminum 5052 is a better choice in most cases when bending aluminum. Copper has a high ductility which makes it easy to bend and shape. Stainless steels are strong and usually easy to bend without cracking. Mild steel is also a strong and economical metal that is easy to bend in many cases without cracking. Titanium is strong and lightweight – it can also be bent though it is less often used for bending. Brass has good ductility and is easy to bend. Even difficult metals can be bent in most cases if a large enough radius is provided in comparison to the thickness but tooling for large radius bends can add to cost.
How sheet metal fabrication machines are programmed
CNC (Computer Numerical Control) machines are programmed using a specialized programming language called G-code. G-code is a standardized programming language that tells the CNC machine where to move the cutting tool, how fast to move it, and what path to follow.
To program a CNC machine, the programmer will typically start by creating a 3D model of the part they want to produce using computer-aided design (CAD) software. The programmer will then use CAM (Computer-Aided Manufacturing) software to generate the G-code instructions based on the 3D model and the specific tool paths required to machine the custom metal part.
Once the G-code has been generated, it can be loaded into the CNC machine’s controller and the machine will follow the instructions to produce the part.
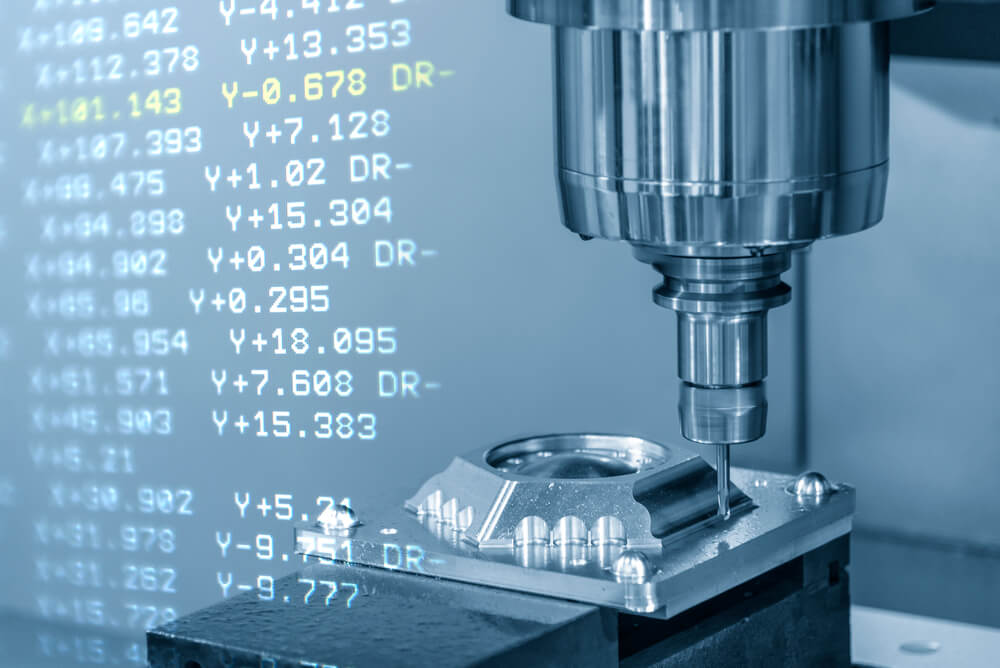
Sheet metal fabrication accuracy
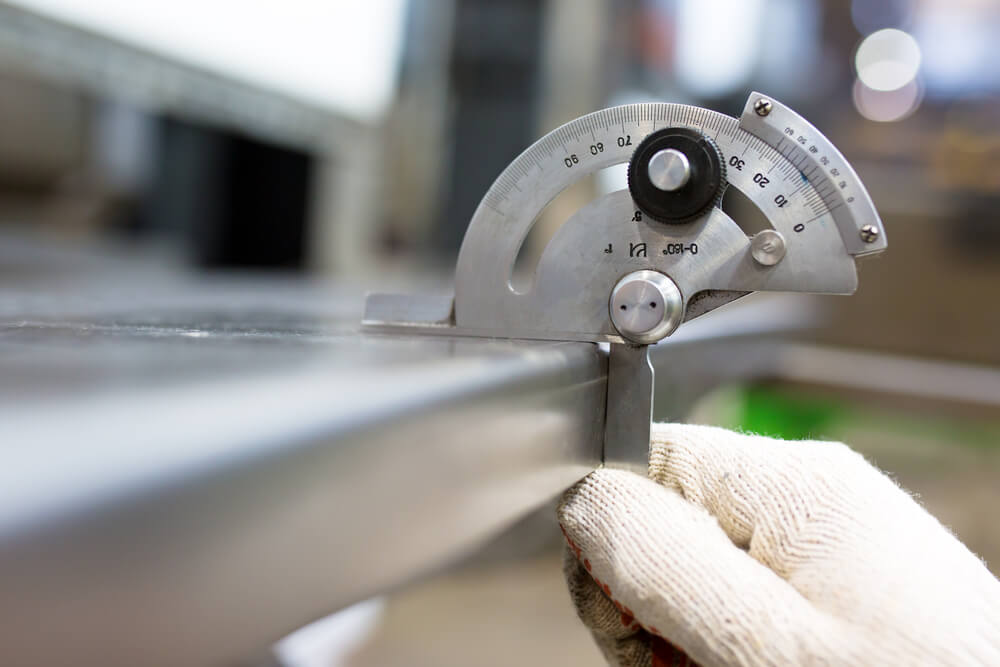
The accuracy and precision of sheet metal fabrication depends on a number of factors, including the quality of the machine itself, the skill of the operator, and the sheet metal design of the parts being produced. In general, fabrication machines are capable of producing parts with very high levels of accuracy, but the actual level of accuracy will depend on the specific machine and the particular application.
Many fabrication machines are designed to be accurate to within a few thousandths of an inch (0.001 inches).
Even the best CNC machines are limited to the tools and fixtures being used and the quality of the raw materials being machined.
Sheet Metal Finishes
Surface finishing is a process that is used to improve the appearance and functionality of custom 2D metal parts. It is an important step in the manufacturing process, as it helps to improve the quality of the part and can help to improve the strength, wear resistance, and corrosion resistance of the part, as well as giving it a unique cosmetic appearance.
There are several ways to finish or coat cut sheet metal parts after fabrication:
- Painting can be used to finish metal sheet parts.
- Powder coating involves applying a dry powder paint to the parts, which is then baked onto the part. This method is often used for parts that need to be used in a harsh environment.
- Anodizing creates a durable, corrosion-resistant finish on aluminum parts. This is a chemical and electrical process which causes a thin oxide layer to form on the surface of the parts.
- Electroplating involves applying a thin layer of metal to the surface of the parts.
- Passivation creates a corrosion-resistant finish on stainless steel parts.
- Polishing uses abrasive materials to create a smooth, shiny surface finish on the parts.
The choice of finish or coating depends on the requirement of the part, the environment it will be used in, and the desired appearance.
How to choose the right fabrication process for a specific project?
- Laser cutting is ideal for thinner sheets and is both economical and precise.
- Waterjet cutting is ideal for thickener materials and also can cut plastics and almost any material.
- Plasma cutting is ideal for thicker metals in parts that can tolerate rougher edges – it is usually one of the most economical options for thick metals.
How do you choose the right sheet metal fabrication company for a project?
There are several factors to consider when choosing a precision sheet metal manufacturer:
- Select a vendor with substantial experience in manufacturing services.
- Make sure they have the right equipment and skill to meet the part specifications.
- Compare the price of their service and delivery time.
- Check that the vendor has a good record of producing high-quality products.
- Select one that has good communication and customer service.
- Verify that they understand your needs.
- If your project requires frequent visits or local delivery, it may be beneficial to choose a local company.
Designing for sheet metal
When designing for custom sheet metal fabrication, some of the factors that you need to specify include: material type, thickness, location of bends, angle of bends, tolerance of thickness, tolerance of bends, radius of bends, location of a features, tapped hole specs, finish, hardware to be assembled if needed and any other other relevant specs. Some CAD software, such as eMachineShop CAD has all those specifications built into the software to guide you.
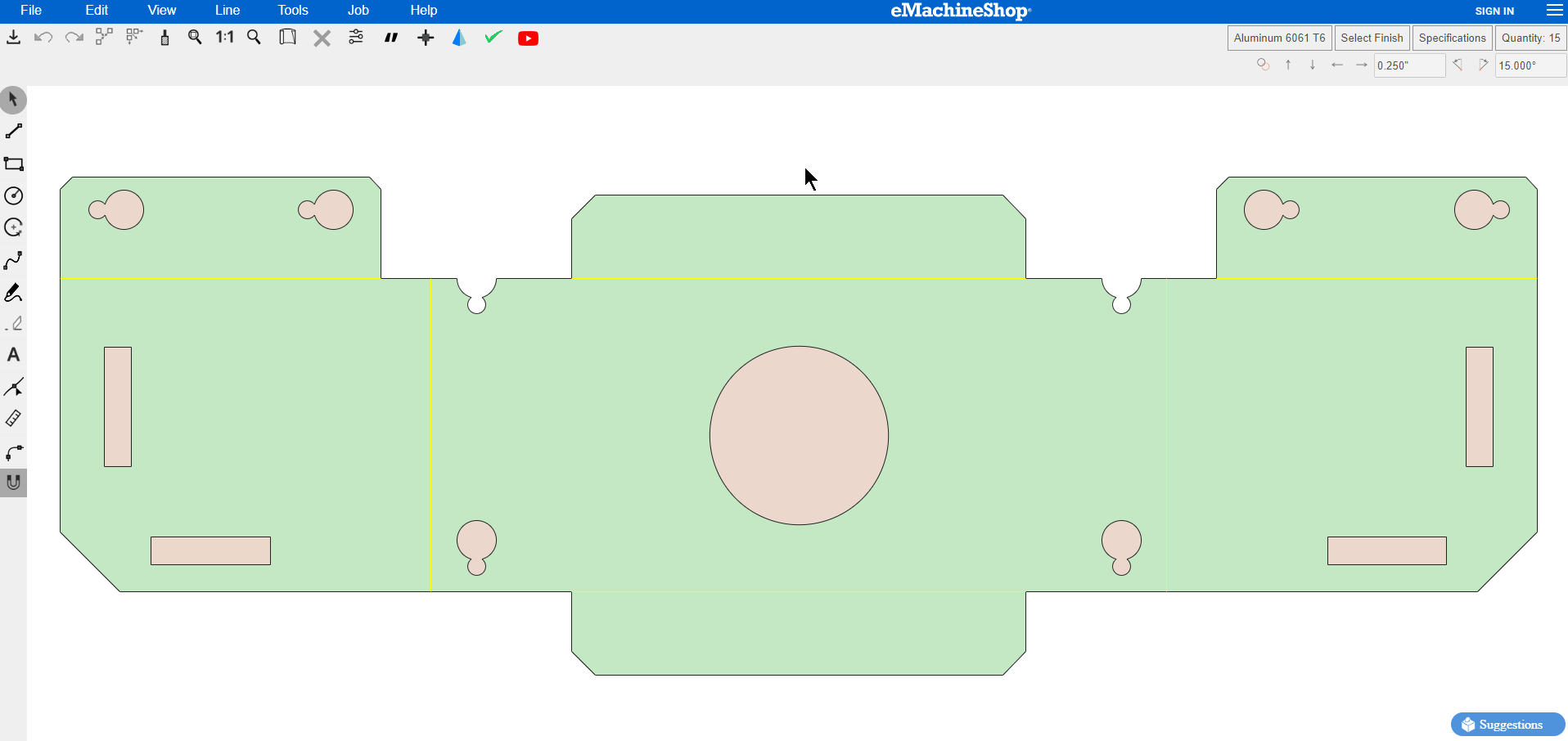