Introduction
In the vast and varied landscape of manufacturing, custom sheet metal fabrication emerges as a pivotal force, driving innovation and precision across countless industries. From the delicate intricacies required in aerospace components to the robust durability demanded in construction, the art of transforming sheet metal into precise, functional forms is both complex and captivating. This exploration delves deep into the realm of custom sheet metal fabrication, shedding light on the cutting-edge techniques, indispensable tools, and expert finishing processes that together define the excellence of this field.
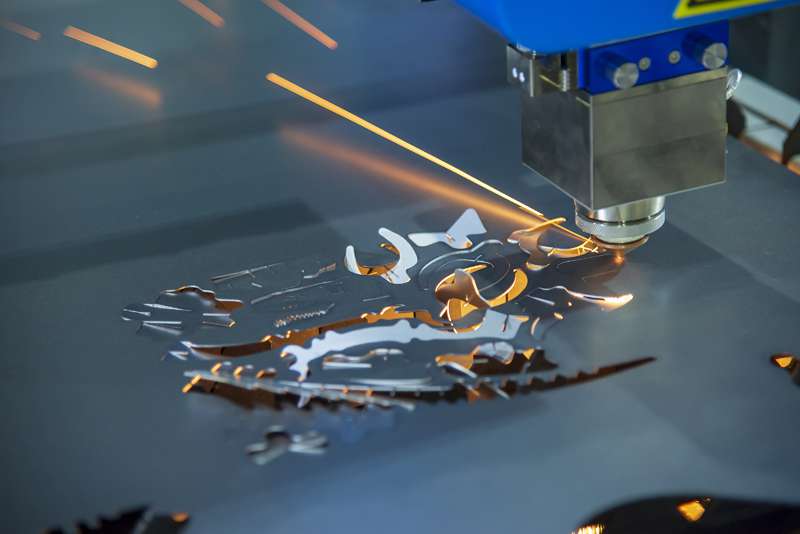
Understanding Sheet Metal Fabrication
At its core, sheet metal fabrication is a multifaceted process that spans cutting, bending, and assembling metal to craft products and components of varied complexity and design. This foundational pillar of manufacturing combines strength with flexibility, enabling the creation of structures that are both durable and adaptable. The essence of sheet metal fabrication lies not only in manipulating material properties but also in the creative vision that guides the transformation of metal sheets into finished products.
Sheet Metal Fabrication Techniques
The journey of fabrication begins with cutting, where large metal sheets are divided into smaller pieces or intricately shaped according to project specifications. This critical first step has evolved significantly, embracing technologies that range from traditional shearing to state-of-the-art laser cutting, waterjet cutting, and plasma cutting services. Each technique offers unique advantages, catering to specific material types and precision requirements, setting the stage for the ensuing fabrication process. For a good short article for choosing the right metal cutting process for sheet metal fabrication, the Metal Forming Magazine offers valuable insights.
Laser Cut Parts: Unparalleled in precision, laser cutting services utilize focused light beams to make intricate cuts with exceptional accuracy, making it ideal for complex designs and detailed work.
Waterjet Cutting Service: For materials sensitive to high temperatures, waterjet cutting provides a versatile, cold-cutting alternative, employing high-pressure water mixed with abrasive particles to slice through metal without altering its intrinsic properties.
Plasma Cutting Service: Excelling in speed and efficiency, plasma cutting uses ionized gas to cut through electrically conductive materials, offering a cost-effective solution for thicker metal sheets.
Advanced Bending Techniques in Sheet Metal Fabrication
CNC Press Brake Operation
At the heart of modern bending technology lies the CNC press brake operation. This cornerstone of precision fabrication offers unmatched accuracy and repeatability, revolutionizing how metal is shaped. Computer-controlled to execute detailed bending instructions, CNC press brakes ensure each fold aligns perfectly with the project’s specifications, embodying the essence of precision bending solutions.
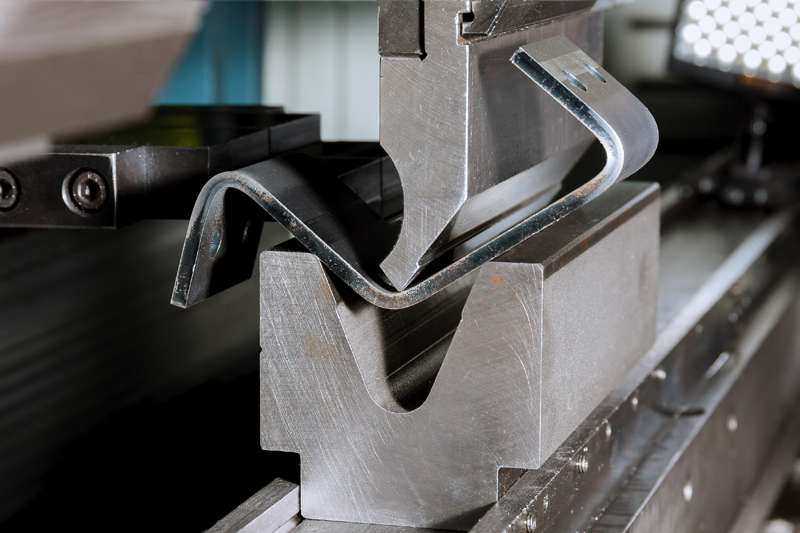
Automated Sheet Metal Bending
The shift towards automation in sheet metal bending marks a significant advancement in the field. By reducing reliance on manual labor, automated sheet metal bending technologies like high-speed press brakes streamline production processes, increase efficiency, and maintain consistent quality across extensive production runs.
Sheet Metal Bending Techniques
Sheet metal bending is an art form that utilizes various techniques—air bending, bottoming, and coining—to achieve desired shapes and angles. Each method offers unique benefits, catering to different material types and application requirements. This flexibility underscores the adaptability of metal fabrication processes to accommodate intricate designs and complex metal forms, driving the continuous optimization of bending operations.
Joining: The Art of Unity
The final act of fabrication is the assembly, where individual pieces merge to form a unified structure. This phase employs various techniques such as welding, riveting, and the use of adhesives, each selected based on the strength requirements and the final application. The integrity of the joining process is paramount, as it determines the durability and reliability of the fabricated product.
Welding in Sheet Metal Fabrication
Welding, a fundamental process in joining metal components, utilizes heat, pressure, or a combination of both to meld pieces together, creating a seamless and strong bond.
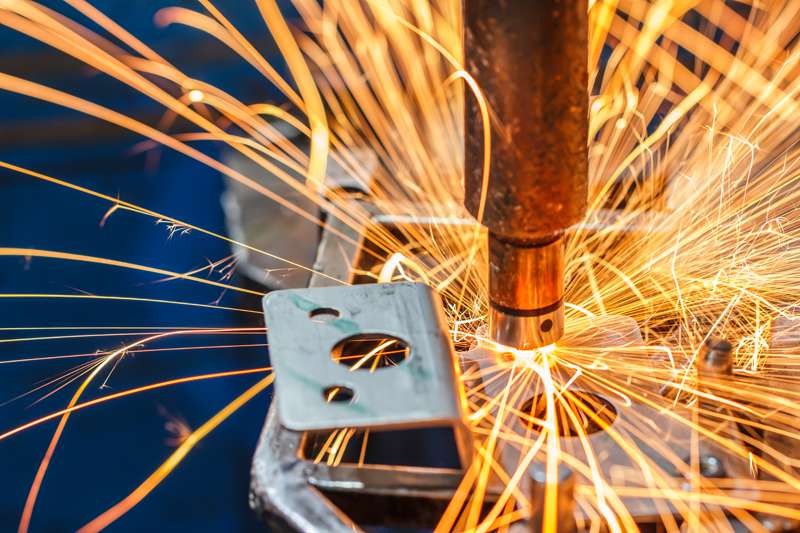
Three Popular Welding Methods
TIG Welding (Tungsten Inert Gas Welding)
Precision TIG welding stands out for its control and accuracy, making it ideal for detailed welds on thinner materials. This method is particularly suited for custom fabrication projects that demand high-quality finishes and strong, visually appealing joints. TIG welding’s versatility across various materials, including aluminum and stainless steel, further enhances its application in diverse manufacturing scenarios.
MIG Welding (Metal Inert Gas Welding)
Known for its speed, MIG welding addresses the need for efficient production without compromising joint integrity. The advent of automated MIG welding systems has revolutionized large-scale fabrication projects, ensuring uniformity and speed. Its robust joining capabilities make MIG welding a go-to method for working with thicker materials across a range of industries. Read this article on Bob Vila for a great review of TIG vs MIG welding.
Stick Welding (Shielded Metal Arc Welding)
Stick welding’s simplicity and effectiveness in outdoor or windy conditions make it invaluable for field repairs and heavy material applications. Recent advancements have improved stick welding techniques, making it more efficient and versatile for a wide array of metals.
Sheet Metal Fabrication Tools and Equipment
The evolution of tools and equipment has been a game-changer in sheet metal fabrication, expanding the realm of possibilities. From laser cutters known for their precision and finesse to CNC press brakes that promise accuracy and flexibility, the modern fabricator’s toolbox is a testament to technological advancement. Turret punches and versatile welding stations further complement the fabricator’s arsenal, enabling a broad spectrum of fabrication tasks to be accomplished with precision and efficiency.
Finishing Techniques: The Final Flourish
Powder Coating: A Durable Embrace
Powder coating stands out as a premier finishing technique, offering a durable, protective, and aesthetically pleasing layer to metal products. This process involves the electrostatic application of dry powder, followed by curing under heat to form a hard coat that resists scratches, chipping, and fading. Beyond its functional benefits, powder coating is celebrated for its minimal environmental impact, making it a favored choice in eco-conscious manufacturing circles.
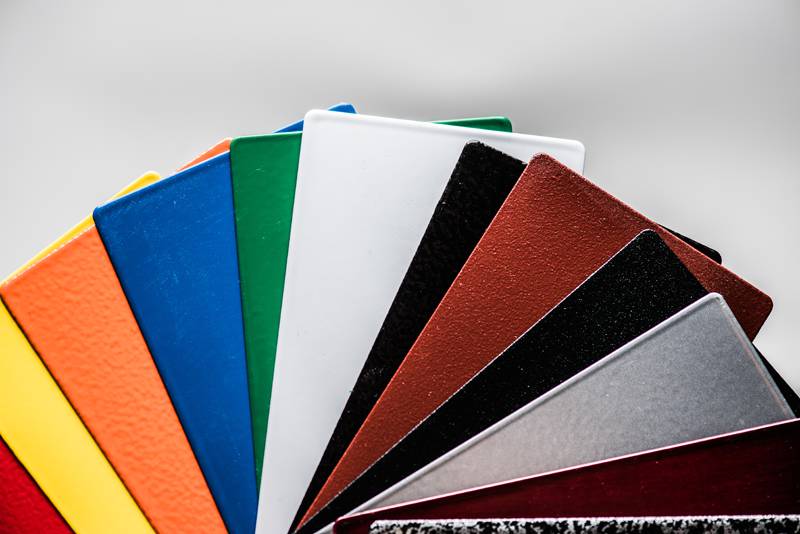
Anodizing: The Aluminum Alchemy
Specifically suited to aluminum parts, anodizing transforms the surface into a corrosion-resistant, anodic oxide finish. This electrochemical process not only fortifies aluminum against wear and tear but also allows for color customization, enhancing both the material’s durability and visual appeal. Anodizing represents a harmonious blend of protection and aesthetics, providing an additional layer of sophistication to aluminum products.
Applications of Sheet Metal Fabrication
Aircraft and Aircraft Ground Support Equipment (GSE)
In the aerospace sector, the demand for precision and reliability is unparalleled. Laser cut parts are crucial here, offering the exactitude necessary for the intricate components of aircraft and their ground support equipment (GSE). These parts must withstand extreme conditions and stress, making the precision of laser cutting services and the robustness of plasma cutting services integral to their fabrication. The durability and precision of these cutting methods ensure that components meet the strict safety and performance standards required in aviation, from the structural elements of the aircraft to the specialized machinery used in GSE.
Automotive Industry
The automotive industry relies heavily on laser cut parts for manufacturing vehicles that are both safe and aesthetically pleasing. The precision offered by laser cutting services is essential for creating intricate designs and ensuring the perfect fit of each component, from the engine parts to the decorative trim. Plasma cutting services also play a role in crafting larger, more robust pieces that form the vehicle’s frame and body, showcasing the versatility of sheet metal fabrication in accommodating both functional and design needs of the automotive sector.
Construction
In construction, the strength and malleability of sheet metal make it a material of choice for various applications, from structural supports to roofing and siding. Plasma cutting services are invaluable in this industry, enabling quick and efficient cutting of large metal sheets into precise shapes and sizes needed for building structures. The adaptability of sheet metal, combined with the precision of cutting services, facilitates the creation of durable, custom-designed elements that contribute to the aesthetic and functional integrity of buildings.HVAC Systems
The HVAC industry benefits significantly from advancements in sheet metal fabrication, particularly in the manufacturing of ductwork and ventilation components. Laser cut parts provide the accuracy necessary for creating efficient airflow systems, ensuring that components fit together seamlessly to improve energy efficiency and indoor air quality. The use of laser cutting services in this field highlights the importance of precision in producing complex shapes and designs required for modern HVAC solutions.
Appliance Manufacturing
Sheet metal fabrication is a cornerstone of the appliance industry, where it’s used to create everything from refrigerators to washing machines. The ability to produce laser cut parts with high precision is essential for the aesthetic appeal and functionality of household appliances. Plasma cutting services, on the other hand, offer the versatility needed to shape larger components, demonstrating the critical role of advanced cutting techniques in meeting the diverse manufacturing needs of this sector.
Medical Devices
The medical industry demands the highest standards of precision and hygiene for its devices, making laser cutting services a preferred choice. The ability to create intricate, laser cut parts with smooth edges is vital for manufacturing devices that are safe for patient use. The precision of these parts is crucial not only for the functionality of medical devices but also for their durability and ease of sterilization, underscoring the importance of advanced sheet metal fabrication techniques in healthcare.
Industrial Machinery
In the realm of industrial machinery, plasma cutting services stand out for their ability to handle thick materials required for heavy-duty equipment. The strength and precision provided by laser cut parts are also critical in creating components that withstand the rigors of industrial use. The versatility and efficiency of sheet metal fabrication are evident in the production of machinery that powers manufacturing processes worldwide, showcasing the adaptability of these techniques to meet varied industrial needs.
Conclusion: Mastering the Art and Science of Fabrication
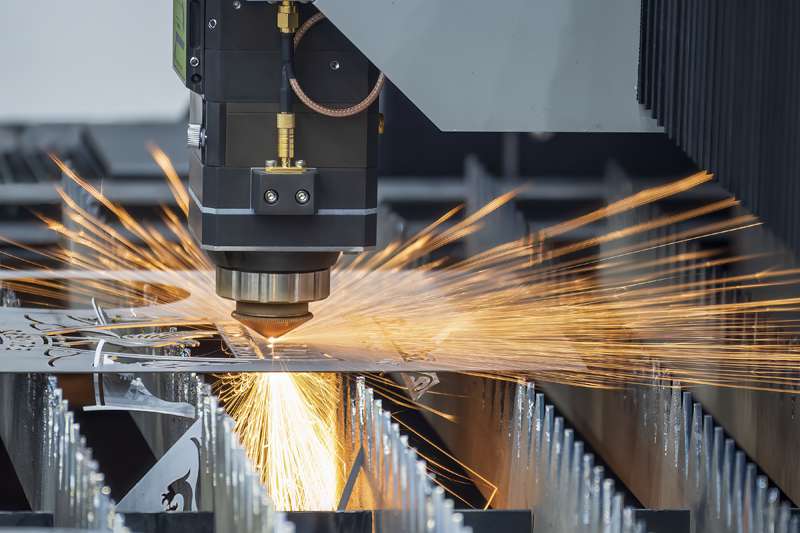
Sheet metal fabrication stands as a cornerstone of modern manufacturing, blending skill, technology, and creativity to meet the evolving demands of design and functionality. By mastering advanced techniques and leveraging the latest technologies, custom sheet metal fabrication stands as a pillar of the manufacturing world, offering solutions that meet the ever-evolving demands of design and functionality. The fusion of skill, technology, and creativity in this field opens up new horizons for custom manufacturing projects, setting new standards for quality and innovation in the world of metalwork.
For help with your next sheet metal fabrication project and to explore cnc bending service, online waterjet cutting services, online laser cutting services for custom laser cutting, plasma cutting service, and sheet metal finishing options, contact us at techsup@emachineshop.com or visit https://www.emachineshop.com/quote/ for a quote. Our team of experts is ready to assist you in bringing your designs to life with precision and quality, utilizing the latest in sheet metal fabrication technology.